❖本調査資料に関するお問い合わせはこちら❖
素材や印刷技術における著しい技術革新により、日本の3Dプリント市場は発展を遂げています。日本企業は、高精度3Dプリンターの開発や、金属、セラミック、バイオ素材など素材の選択肢拡大に多額の投資を行っています。こうした進歩は、カスタマイズされた複雑な部品生産を必要とする自動車や医療などの産業に貢献しています。例えば、2024年2月には、日本通運ホールディングスが、NXグローバルイノベーションファンドを通じて、AI技術を活用した手頃な価格の3Dプリント義足を提供する日本のスタートアップ企業、インスタリンブ社に出資しました。この投資は、インスタリンブ社のアジアや新興市場での事業拡大を支援し、高品質な義肢へのアクセスを改善することで社会課題の解決を図り、持続可能な社会発展を促進することを目的としています。さらに、3DプリントプロセスにAIとIoTを統合することで、効率性と製品品質が向上し、迅速なプロトタイピングと製造のための望ましいソリューションとなります。
日本政府は、資金援助、補助金、研究協力などを通じて、3Dプリントの導入を積極的に支援しています。これらの取り組みは、先進的な製造能力を強化し、国際競争力を高めることを目的としています。中小企業(SME)における付加製造の統合を奨励するプログラムは特に大きな影響力を持ち、エレクトロニクスやロボット工学などの分野におけるイノベーションを可能にしています。さらに、公的機関と民間企業とのパートナーシップにより、最先端の3Dプリント技術の開発が促進され、市場の拡大がさらに加速しています。例えば、2024年11月には、日本政策投資銀行(DBJ)が、合金開発と金属3Dプリントを専門とする英国の新興企業Alloyed Limitedに投資を行いました。この投資は、Alloyed社の材料インフォマティクス(MI)技術と日本および英国での事業拡大を支援するものであり、技術革新と、日本の冶金および製造業の近代化に向けたコラボレーションの促進に重点的に取り組んでいるDBJの姿勢に沿うものです。
日本の3Dプリント市場の動向:
金属3Dプリントの用途拡大
日本は、航空宇宙、自動車、製造などの高性能分野での応用により、金属3Dプリンティングに対する幅広い需要を見込んでいます。 先進的な付加製造技術への企業による投資の増加は、軽量で耐久性があり、複雑な部品の製造に重要な役割を果たしています。 例えば、2024年9月には、ロサンゼルスに拠点を置く付加製造企業3DEOが、みずほ銀行のトランジション・インベストメント・ファシリティを通じて350万米ドルの投資を確保しました。この資金調達は、3DEOによるAI主導の設計、インテリジェント・レイヤリング、および付加製造向け設計(DfAM)の統合を支援することを目的としており、イノベーションと持続可能な生産を強調しています。これらの進歩は、精密工学と環境に配慮した持続可能な実践に対する日本の取り組みと密接に一致しており、金属3Dプリントの採用をさらに促進しています。
医療分野における3Dプリントの使用拡大
日本では、3Dプリンティングの医療分野での利用が急速に拡大しており、特にカスタムメイドの義肢、歯科インプラント、手術器具などの分野で利用が進んでいます。例えば、2024年5月には、UNIDOが日本政府と協力し、「ウクライナにおける3Dプリント義肢と雇用創出のための緊急支援」プロジェクトを開始しました。この取り組みでは、ウクライナの義肢装具士を訓練し、施設に先進的な3Dプリンティング技術を導入し、紛争の影響を受けた人々に高品質の義肢を提供しています。これにより、移動の自由を向上させ、持続可能な雇用機会を創出し、ウクライナの社会経済成長を支援することを目指しています。患者に合わせたソリューションを創出できる技術により、治療効率が向上します。医療機関と3Dプリンティング企業との連携により、イノベーションがさらに推進され、ヘルスケアは市場で最も急速に成長している分野の1つとなっています。
環境にやさしい素材の採用が増加
日本のメーカーは、持続可能性への取り組みを反映し、環境への影響を低減するために、3Dプリントにおいて環境にやさしくリサイクル可能な素材の使用を優先しています。例えば、2024年10月には、日本のテクノロジー企業である旭化成が、イタリアのAquafil S.p.A.と提携し、Aquafilの再生ポリアミド6(PA6)であるECONYLポリマーと旭化成のセルロースナノファイバー(CNF)を組み合わせた新しい3Dプリント素材を開発しました。この高強度で成形可能な複合素材は、自動車や航空機への応用が期待されています。このようなバイオベースおよび生分解性素材のイノベーションは勢いを増しており、世界的な持続可能性の目標を達成しようとする産業に、より環境にやさしい代替策を提供しています。さらに、こうした進歩は、持続可能性を先進的な製造技術に統合する日本のリーダーシップを際立たせています。
日本の3Dプリンティング産業の区分:
IMARC Groupは、日本の3Dプリンティング市場の各セグメントにおける主要なトレンドの分析を提供し、2025年から2033年までの国および地域レベルでの予測を行っています。市場は、技術、プロセス、材料、製品、用途、エンドユーザーに基づいて分類されています。
技術別の分析:
ステレオリソグラフィー
溶融堆積モデリング
選択的レーザー焼結
電子ビーム溶解
デジタルライトプロセッシング
その他
ステレオリソグラフィー(SLA)は、その精度と滑らかな表面仕上げにより医療用途に最適であることから、3Dプリント業界で広く使用されています。UV光を使用して樹脂を層ごとに硬化させることで、SLAは精密なデザインの作成に優れています。歯科用モデルやプロトタイプの製造に、ヘルスケアや自動車産業などのさまざまな分野や消費財がこの技術を利用しています。
FDM(Fused deposition modeling)は、日本の3Dプリント市場で広く利用されている、コスト効率の高い多目的技術です。この方法では、溶融した熱可塑性樹脂を層ごとに押し出して、機能部品やプロトタイプを製造します。家電、教育、製造など、さまざまな分野で軽量部品の製造にFDMが活用されています。また、日本の企業はエコ素材に注目しており、持続可能性の目標をサポートするためにFDM技術の改良に取り組んでいます。
選択的レーザー焼結(SLS)は、産業用および高性能用途に重点を置く日本の印刷業界における革新的な技術であり、ポリマーや金属などの材料をレーザーで溶融し、層ごとに積層します。その結果、航空宇宙、自動車、医療などの産業向けの頑丈で複雑な部品が作成され、試作品や最終製品の製造にSLSが活用されています。さまざまな材料やプロセスの有効性に関する継続的な改善により、日本での利用が広がっています。
電子ビーム溶解(EBM)は、日本の航空宇宙および医療分野において、電子ビームを真空条件下で粉末金属に照射して溶解し、機械的特性に優れた部品を製造する役割を果たしています。EBMは、タービンブレード、インプラント、および精度と強度が求められるその他の重要な部品の製造に特に適しています。日本の企業は、製造上の課題に対処し、最高品質の部品の生産性を向上させるために、EBMに注目しています。
デジタル光造形(DLP)は、3Dプリント業界でますます人気が高まっており、日本では、モデルやオーダーメイドのジュエリーアイテムの製作など、細部や鮮明な解像度が求められる作業で利用されています。この技術では、プロジェクターを使用して樹脂の層を迅速かつ正確に固めていきます。医療や消費財など、さまざまな分野で、デザインの作成や表面仕上げにDLP技術が活用されています。日本企業は、DLPシステムの改良により、素材の選択肢を広げ、生産スピードを向上させることで、市場での存在感を強固なものにしようとしています。
プロセス別分析:
バインダージェッティング
指向性エネルギー堆積
材料押出
材料噴射
パワードベッド融合
シート積層
バット光重合
バインダージェッティングは、3Dプリント業界で人気が高まっており、日本では、金属やセラミック部品を正確かつ効率的に製造するために使用されています。この方法では、バインダーを使用して材料を結合させるため、自動車や航空宇宙分野で使用される軽量かつコスト効率の高い部品の製造が可能です。 バインダージェット方式の利点のひとつは、サポート構造を追加することなく形状を製造できる点であり、試作品や小規模生産に非常に適しています。 日本企業は、互換性を向上させ、生産プロセスを迅速化するための研究に投資し、さまざまな業界での利用拡大を目指しています。
指向性エネルギー堆積法(DED)は、日本の航空宇宙および自動車産業において、高性能金属部品の製造や修理に広く用いられている3Dプリントの主要なプロセスです。この技術では、集束熱エネルギーを使用して材料を溶融し堆積させるため、大型で複雑な部品の製造が可能です。日本の企業は、特にカスタマイズされた設計や構造修理を必要とする用途において、金属部品製造の精度と効率性を求めてDEDを活用しています。DED技術の進歩は、その採用をさらに促進し、日本の積層造形の分野におけるその重要性を際立たせています。
日本の印刷業界では、材料押出は、試作品の作成や、溶融した材料を層ごとに堆積させることで効率的に消費財を製造するなど、さまざまな目的で使用される技術です。特に、大手メーカーや中小企業(SME)の両方にとって、特定の設計要件や好みに応じたプラスチック部品の製造に効果的です。生分解性材料への関心の高まりが、持続可能性を優先する日本の製造業界において、この分野の進歩を後押ししています。
マテリアルジェッティングは、日本のヘルスケアおよび消費財業界で評価されている高精度の3Dプリントプロセスです。このプロセスでは、ビルドプラットフォーム上に材料の液滴を堆積させることで、細かいディテールや滑らかな表面仕上げを実現し、歯科用モデル、ジュエリー、カスタマイズされたプロトタイプに最適です。日本の企業は、精度と材料効率を向上させるためにマテリアルジェッティング技術を進化させています。1回のプリントで複数の材料を使用できる機能により、複雑なデザインや詳細なテクスチャを必要とする用途での採用がさらに加速しています。
パウダーベッド溶融結合(PBF)は、日本の3Dプリント市場で広く利用されており、特に航空宇宙、自動車、医療の各業界で活用されています。このプロセスでは、レーザーまたは電子ビームを使用して粉末材料を選択的に溶融し、層ごとに積層することで、複雑で高強度の部品を製造します。PBFは軽量かつ耐久性のある部品の製造をサポートしており、精密工学を重視する日本のニーズに合致しています。材料の互換性とプロセス効率の継続的な向上により、産業用途での採用がさらに加速しています。
シート積層は、日本では特殊な3Dプリントプロセスとして知られており、紙、プラスチック、金属などの素材からコスト効率の高い積層造形物を製造する際に使用されます。このプロセスでは、薄い素材シートを結合して軽量かつ耐久性のある部品を製造します。日本のメーカーは、この手法をパッケージング、工業デザイン、プロトタイピングなどの用途に活用しています。エネルギー消費量と材料コストが低いことから、持続可能な選択肢であり、環境に配慮した製造ソリューションを推進する日本の取り組みとも一致しています。
バット光重合は、義肢、インプラント、外科手術用モデルなどの高精度部品の製造において、日本の医療および歯科業界で重要なプロセスとなっています。この方法では、UV光を使用して液状樹脂を層ごとに硬化させるため、非常に精密で滑らかな仕上げが可能です。日本企業は、このプロセスを進化させ、樹脂の特性を改善し、その用途を拡大しています。材料の無駄を最小限に抑えながら複雑な形状を造形できることから、光重合は、精密さが重視される日本の高品質な3Dプリント市場において重要な役割を果たしています。
材料別分析:
光重合樹脂
プラスチック
金属およびセラミック
その他
光重合樹脂は、日本の3Dプリント市場における主要材料であり、医療や消費財などの業界で、非常に精密で正確なプロトタイプの作成に広く使用されています。これらの材料は、紫外線で硬化し、歯科用機器や宝飾品の金型など、精密さが求められる用途に適しています。日本のメーカーは、耐久性と柔軟性を高める先進的な光重合性組成物の開発に重点的に取り組んでおり、多様な産業ニーズに応えています。光重合性樹脂の採用が拡大していることは、ラピッドプロトタイピングや小ロット生産における高品質な出力の実現において、その重要性が強調されています。
プラスチックは、日本の3Dプリント市場の要であり、自動車、エレクトロニクス、ヘルスケア産業における用途での適応性とコスト効率の高さが評価されています。 ABS、PLA、ナイロンなどの一般的な材料は、プロトタイピングや機能部品の製造に広く使用されています。 日本企業は、持続可能性の目標を達成するために、生分解性およびリサイクル可能なプラスチックの革新を優先しています。 軽量で耐久性があり、カスタマイズ可能なソリューションへの需要の高まりにより、日本の付加製造エコシステムにおけるこの材料セグメントの継続的な拡大が確実視されています。
金属とセラミックは、日本の3Dプリント市場における高性能素材であり、主に航空宇宙、自動車、医療の各分野で使用されています。軽量かつ耐久性のある部品の製造には、チタン、アルミニウム、ステンレス鋼などの金属材料が不可欠であり、セラミックは高温用途に優れています。日本のメーカーは、粉末床溶融結合(PBF)や指向性エネルギー堆積(DED)などの先進技術を活用し、これらの素材を精密工学向けに最適化しています。持続可能で高強度の金属およびセラミックのオプション開発に重点的に取り組むことは、産業用3Dプリントにおけるそれらの重要性を強調しています。
製品別分析:
プリンター
材料
ソフトウェア
サービス
プリンターは、日本における3Dプリント市場の基盤であり、デスクトップモデルから産業用モデルまで、幅広い機器が含まれます。日本のメーカーは、自動車やヘルスケアなど、多様な業界に対応するために、金属やマルチマテリアルプリンターなどの先進技術に多額の投資を行っています。精密性、耐久性、効率性の重視がプリンターの設計と機能におけるイノベーションを推進しています。このセグメントは、プロトタイピング、工具、機能部品の製造に3Dプリンティング技術を採用する企業にとって重要な役割を果たしています。
材料は、日本における3Dプリント市場の主要推進要因であり、持続可能で高性能なオプションへの注目が高まっています。金属、ポリマー、セラミック、環境にやさしい複合材料などの材料は、航空宇宙、自動車、医療などの幅広い用途で使用されています。日本のメーカーは、世界的な持続可能性の目標を達成するために、リサイクル可能な材料やバイオベースの材料を積極的に開発しています。このセグメントは、軽量で耐久性があり、複雑な部品の生産をサポートしており、3Dプリントの用途の拡大と多様化に不可欠です。
ソフトウェアは、効率的な設計、モデリング、最適化プロセスを可能にする、日本における3Dプリンティングエコシステムに不可欠な要素です。先進的なソフトウェアソリューションは、AIと材料インフォマティクスを統合し、精度とカスタマイズ性を向上させます。日本企業と研究機関は、ワークフローの合理化、生産品質の向上、コスト削減を実現するツールの開発で協力しています。シミュレーションとリアルタイムモニタリングソフトウェアの採用は、航空宇宙、ヘルスケア、消費財などの業界における付加製造のイノベーションを支えています。
日本における3Dプリント市場では、専門知識のアウトソーシング、メンテナンス、カスタム生産に対する需要の高まりに対応するサービスが提供されています。各企業は、設計支援、プロトタイピング、製造サポートを含む総合的なソリューションを提供しています。リコーの「All-In 3D Print」のようなマネージドサービスは、企業が社内リソースを必要とせずに、エンドツーエンドの3Dプリントソリューションを利用できるようにします。このセグメントの成長は、さまざまな業界で3Dプリントサービスの導入が加速し、生産効率が向上していることを反映しています。
用途別分析:
プロトタイピング
ツーリング
機能部品製造
プロトタイピングは、日本における3Dプリント市場を牽引する主要な用途であり、さまざまな業界で製品モデルを迅速かつコスト効率よく開発することを可能にします。積層造形法により、従来の方法では困難だった複雑な設計による高精度なプロトタイプ作成が可能になります。 自動車、航空宇宙、家電製品などの分野におけるイノベーションサイクルを加速し、設計プロセスの最適化を図りながら市場投入までの時間を短縮します。 3Dプリント技術の柔軟性により、企業はプロトタイプのテストと改良を効率的に行うことができ、日本の高品質で精密なエンジニアリング製品への注力をサポートします。
日本では、3Dプリントは金型、治具、固定具の効率的な生産に大きく貢献しています。 積層造形は、従来の金型製造方法に関連するリードタイムとコストを削減しながら、複雑なツールのための複雑な設計を可能にします。 自動車、電子機器、航空宇宙などの産業は、製造の効率性と精度を向上させるために3Dプリントされた金型に依存しています。 軽量で耐久性のあるツールを作成する能力は、持続可能で高度な生産プロセスを重視する日本をサポートしています。
機能部品の製造は、日本における3Dプリント市場で成長している用途であり、ヘルスケア、航空宇宙、自動車などの業界における最終用途部品のニーズに対応しています。 積層造形法では、材料の無駄を削減しながら軽量で高性能な部品を製造することができます。 また、特定の業界のニーズに応えるカスタマイズや小ロット生産も可能です。 日本の製造業者は、効率性、耐久性、持続可能性を高めるために機能部品の3Dプリントを導入するケースが増えており、これは先進的な製造手法への移行を目指す世界的なトレンドに沿ったものです。
エンドユーザー別分析:
消費財
機械
ヘルスケア
航空宇宙
自動車
その他
日本の3Dプリント市場における消費財は、カスタマイズされた革新的な製品をコスト効率よく製造するために、付加製造を活用しています。企業は3Dプリントを活用して、プロトタイプやファッションアクセサリー、家庭用品などを高精度かつ迅速に製造しています。ウェアラブル技術や装飾品などのパーソナライズされた製品に対する需要が、この分野の成長を牽引しています。3Dプリンティング技術が進化するにつれ、消費者向け製品の設計や生産におけるその利用は拡大し、より迅速な製品開発サイクルを実現し、独自性、持続可能性、審美性を備えた製品に対する市場の需要に応えています。
日本の機械メーカーは、3Dプリンティングを幅広く採用し、複雑な部品の生産効率を高め、リードタイムを短縮しています。 積層造形法により、従来の方法では製造が困難な複雑な部品の製造が可能になり、産業用機器や工具の革新を支えています。 精密工学に重点的に取り組んでいる日本の製造業者は、3Dプリンティングを利用して機械の性能と耐久性を向上させています。 この分野は、積層造形法が提供する柔軟性とカスタマイズのメリットを享受しており、日本の3Dプリンティング市場における重要なセグメントとなっています。
医療は、日本における3Dプリント市場の主要な推進要因であり、義肢、歯科インプラント、手術器具、バイオプリンティングなどの用途があります。 付加製造は高度にカスタマイズされたソリューションを提供し、患者の治療結果を改善し、製造コストを削減します。 日本の企業や医療機関は、AIやマテリアルズインフォマティクスなどの先進技術と3Dプリントを統合し、患者に特化した機器を開発する分野で最先端を走っています。革新的で利用しやすいヘルスケアソリューションに対するニーズの高まりにより、この分野は市場拡大に大きく貢献するものと見込まれています。
日本の航空宇宙産業では、厳しい性能および安全基準を満たす軽量かつ高強度の部品の製造に3Dプリントが活用されています。 複雑な形状の製造や材料の無駄を省く上で、積層造形は不可欠であり、これは業界が重視する持続可能性の観点とも一致しています。 航空宇宙産業の大手企業は、3Dプリント企業と提携し、生産プロセスの合理化とイノベーションの加速化を図っています。このセグメントでは、精密性と効率性が重視されており、タービンブレード、エンジン部品、構造部品の製造を中心に、日本の3Dプリント市場における成長の主要分野となっています。
日本の自動車業界は3Dプリントの主要な採用者であり、迅速なプロトタイプ作成、軽量化、部品のカスタマイズに活用しています。 付加製造により、複雑な部品のコスト効率の高い製造が可能になり、電気自動車や自動運転車の進歩を支えています。日本の大手自動車メーカーは、設計の柔軟性を最適化し、市場投入までの時間を短縮するために、3Dプリンティング技術に投資しています。持続可能性とエネルギー効率への注目は、革新的な素材や生産プロセスにおける3Dプリンティングの採用をさらに促進し、自動車セグメントを市場に欠かせない貢献者として位置づけています。
競合状況:
日本の3Dプリント市場は、技術的リーダーシップをめぐって国内外の企業が激しい競争を繰り広げているのが特徴です。日本の大手企業は、市場での競争力を維持し、成長を促進するために、高精度の機械や先進的な素材を含む革新的な3Dプリント技術に投資しています。例えば、2024年10月には、大林組が日本初の3Dプリント耐震建築物「3dpod」を発表しました。この構造物は、従来の補強材を使用せずに、日本の厳しい耐震基準を満たしています。3dpodは、地上構造物のすべての構成部品に先進的な3Dプリント技術を使用し、断熱材と輻射システムを統合しています。この方法により、建設時間、労働力、CO2排出量、材料の無駄を削減することができます。ロボットプリンターが現場で作業を完了し、持続可能性と革新性を示しました。大林組は、建築・エンジニアリング・建設(AEC)業界における3Dプリントの用途拡大を目指しており、熟練労働者不足への対応や、地震地域向けの強靭で環境にやさしい構造物の構築に取り組んでいます。この市場には、専門サービスやニッチな用途を提供する新興企業も参入しています。さらに、業界リーダーと学術機関との連携により、研究開発の進歩が促進されています。各分野で需要が高まる中、市場関係者は、製品差別化、コスト最適化、戦略的提携に重点的に取り組み、急速に進化する環境下で競争優位性を維持しようとしています。
本レポートでは、日本における3Dプリンティング市場の競争環境について、主要企業のプロフィールを詳細に分析した包括的な分析を提供しています。
最新ニュースと動向:
2024年5月、放電加工機および3Dプリンターの日本のメーカーであるソディックは、PBFおよびDED金属3Dプリント技術で知られるイタリアの金属3Dプリンターメーカー、Prima Additiveの9.5%の株式を取得した。この提携は、Prima Additive社の高度な専門知識と強力な欧州ネットワークを活用し、航空宇宙、自動車、宝飾品業界での応用を拡大し、日本、欧州、米国などの主要市場における競争力を強化することを目的としています。
本レポートで回答される主な質問
1. 3Dプリンティングとは何か?
2. 日本の3Dプリンティング市場の規模は?
3. 2025年から2033年の間、日本の3Dプリンティング市場の成長率はどの程度か?
4. 日本の3Dプリンティングの市場を牽引する主な要因は何か?
1 はじめに
2 範囲と方法論
2.1 本調査の目的
2.2 関係者
2.3 データソース
2.3.1 一次ソース
2.3.2 二次ソース
2.4 市場推定
2.4.1 ボトムアップアプローチ
2.4.2 トップダウンアプローチ
2.5 予測方法論
3 エグゼクティブサマリー
4 日本3Dプリンティング市場 – イントロダクション
4.1 概要
4.2 市場力学
4.3 業界トレンド
4.4 競合情報
5 日本3Dプリンティング市場の概観
5.1 過去および現在の市場トレンド(2019年~2024年
5.2 市場予測(2025年~2033年
6 日本3Dプリンティング市場 – 技術別内訳
6.1 ステレオリソグラフィー
6.1.1 概要
6.1.2 歴史的および現在の市場動向(2019年~2024年
6.1.3 市場予測(2025年~2033年
6.2 溶融堆積モデリング
6.2.1 概要
6.2.2 歴史的および現在の市場動向(2019年~2024年
6.2.3 市場予測(2025年~2033年)
6.3 選択的レーザー焼結
6.3.1 概要
6.3.2 過去の市場動向および現在の市場動向(2019年~2024年)
6.3.3 市場予測(2025年~2033年)
6.4 電子ビーム溶解
6.4.1 概要
6.4.2 過去の市場動向および現在の市場動向(2019年~2024年)
6.4.3 市場予測(2025年~2033年)
6.5 デジタルライトプロセッシング
6.5.1 概要
6.5.2 過去の市場動向および現在の市場動向(2019年~2024年)
6.5.3 市場予測(2025年~2033年)
6.6 その他
6.6.1 過去の市場動向および現在の市場動向(2019年~2024年
6.6.2 市場予測(2025年~2033年
7 日本の3Dプリンティング市場 – プロセス別内訳
7.1 バインダージェッティング
7.1.1 概要
7.1.2 過去の市場動向および現在の市場動向(2019年~2024年
7.1.3 市場予測(2025年~2033年)
7.2 指向性エネルギー堆積法
7.2.1 概要
7.2.2 市場の歴史と現在の動向(2019年~2024年)
7.2.3 市場予測(2025年~2033年)
7.3 材料押出法
7.3.1 概要
7.3.2 過去の市場動向および現在の市場動向(2019年~2024年)
7.3.3 市場予測(2025年~2033年)
7.4 材料ジェッティング
7.4.1 概要
7.4.2 過去の市場動向および現在の市場動向(2019年~2024年)
7.4.3 市場予測(2025年~2033年)
7.5 パワーベッドフュージョン
7.5.1 概要
7.5.2 過去の市場動向および現在の市場動向(2019年~2024年
7.5.3 市場予測(2025年~2033年
7.6 シートラミネーション
7.6.1 概要
7.6.2 過去の市場動向および現在の市場動向(2019年~2024年
7.6.3 市場予測(2025年~2033年)
7.7 バット光重合
7.7.1 概要
7.7.2 市場の推移と現状(2019年~2024年)
7.7.3 市場予測(2025年~2033年)
8 日本の3Dプリンティング市場 – 材料別内訳
8.1 フォトポリマー
8.1.1 概要
8.1.2 過去の市場動向と現在の市場動向(2019年~2024年)
8.1.3 市場予測(2025年~2033年)
8.2 プラスチック
8.2.1 概要
8.2.2 過去の市場動向と現在の市場動向(2019年~2024年)
8.2.3 市場予測(2025年~2033年)
8.3 金属およびセラミック
8.3.1 概要
8.3.2 過去の市場動向および現在の市場動向(2019年~2024年)
8.3.3 市場予測(2025年~2033年)
8.4 その他
8.4.1 歴史的および現在の市場動向(2019年~2024年)
8.4.2 市場予測(2025年~2033年)
9 日本の3Dプリンティング市場 – 製品別内訳
9.1 プリンター
9.1.1 概要
9.1.2 過去の市場動向と現在の市場動向(2019年~2024年
9.1.3 市場予測(2025年~2033年
9.2 材料
9.2.1 概要
9.2.2 過去の市場動向と現在の市場動向(2019年~2024年
9.2.3 市場予測(2025年~2033年
9.3 ソフトウェア
9.3.1 概要
9.3.2 市場の歴史と現在の動向(2019年~2024年
9.3.3 市場予測(2025年~2033年
9.4 サービス
9.4.1 概要
9.4.2 市場の歴史と現在の動向(2019年~2024年
9.4.3 市場予測(2025年~2033年)
10 日本の3Dプリンティング市場 – 用途別内訳
10.1 プロトタイピング
10.1.1 概要
10.1.2 市場の歴史と現在の動向(2019年~2024年)
10.1.3 市場予測(2025年~2033年)
10.2 工具
10.2.1 概要
10.2.2 歴史的および現在の市場動向(2019年~2024年
10.2.3 市場予測(2025年~2033年
10.3 機能部品製造
10.3.1 概要
10.3.2 歴史的および現在の市場動向(2019年~2024年
10.3.3 市場予測(2025年~2033年)
11 日本の3Dプリンティング市場 – エンドユーザー別内訳
11.1 消費者向け製品
11.1.1 概要
11.1.2 市場の歴史と現在の動向(2019年~2024年)
11.1.3 市場予測(2025年~2033年)
11.2 機械
11.2.1 概要
11.2.2 歴史的および現在の市場動向(2019年~2024年
11.2.3 市場予測(2025年~2033年
11.3 ヘルスケア
11.3.1 概要
11.3.2 歴史的および現在の市場動向(2019年~2024年
11.3.3 市場予測(2025年~2033年)
11.4 航空宇宙
11.4.1 概要
11.4.2 過去の市場動向および現在の市場動向(2019年~2024年)
11.4.3 市場予測(2025年~2033年)
11.5 自動車
11.5.1 概要
11.5.2 市場の推移と現状(2019年~2024年)
11.5.3 市場予測(2025年~2033年)
11.6 その他
11.6.1 市場の推移と現状(2019年~2024年)
11.6.2 市場予測(2025年~2033年)
12 日本の3Dプリンティング市場 – 地域別内訳
12.1 関東地域
12.1.1 概要
12.1.2 過去の市場動向および現在の市場動向(2019年~2024年
12.1.3 技術別市場内訳
12.1.4 プロセス別市場内訳
12.1.5 材料別市場内訳
12.1.6 製品別市場規模
12.1.7 用途別市場規模
12.1.8 エンドユーザー別市場規模
12.1.9 主要企業
12.1.10 市場予測(2025年~2033年
12.2 近畿地方
12.2.1 概要
12.2.2 歴史的および現在の市場動向(2019年~2024年)
12.2.3 技術別市場規模
12.2.4 プロセス別市場規模
12.2.5 材料別市場規模
12.2.6 製品別市場規模
12.2.7 用途別市場規模
12.2.8 エンドユーザー別市場規模
12.2.9 主要企業
12.2.10 市場予測(2025年~2033年
12.3 中央/中部地域
12.3.1 概要
12.3.2 過去の市場動向および現在の市場動向(2019年~2024年
12.3.3 技術別市場規模
12.3.4 プロセス別市場規模
12.3.5 材料別市場規模
12.3.6 製品別市場規模
12.3.7 用途別市場規模
12.3.8 エンドユーザー別市場規模
12.3.9 主要企業
12.3.10 市場予測(2025年~2033年
12.4 九州・沖縄地域
12.4.1 概要
12.4.2 過去の市場動向および現在の市場動向(2019年~2024年
12.4.3 技術別市場規模
12.4.4 プロセス別市場規模
12.4.5 材料別市場規模
12.4.6 製品別市場規模
12.4.7 用途別市場規模
12.4.8 エンドユーザー別市場規模
12.4.9 主要企業
12.4.10 市場予測(2025年~2033年
12.5 東北地域
12.5.1 概要
12.5.2 歴史的および現在の市場動向(2019年~2024年
12.5.3 技術別市場規模
12.5.4 プロセス別市場規模
12.5.5 材料別市場規模
12.5.6 製品別市場規模
12.5.7 用途別市場規模
12.5.8 エンドユーザー別市場規模
12.5.9 主要企業
12.5.10 市場予測(2025~2033年
12.6 中国地域
12.6.1 概要
12.6.2 過去の市場動向と現在の市場動向(2019年~2024年
12.6.3 技術別市場内訳
12.6.4 プロセス別市場内訳
12.6.5 材料別市場内訳
12.6.6 製品別市場内訳
12.6.7 用途別市場内訳
12.6.8 エンドユーザー別市場内訳
12.6.9 主要企業
12.6.10 市場予測(2025年~2033年
12.7 北海道地域
12.7.1 概要
12.7.2 歴史的および現在の市場動向(2019年~2024年
12.7.3 技術別市場規模
12.7.4 プロセス別市場規模
12.7.5 素材別市場規模
12.7.6 製品別市場規模
12.7.7 用途別市場規模
12.7.8 エンドユーザー別市場規模
12.7.9 主要企業
12.7.10 市場予測(2025年~2033年
12.8 四国地域
12.8.1 概要
12.8.2 歴史的および現在の市場動向(2019年~2024年
12.8.3 技術別市場規模
12.8.4 プロセス別市場規模
12.8.5 材料別市場規模
12.8.6 製品別市場規模
12.8.7 用途別市場規模
12.8.8 エンドユーザー別市場規模
12.8.9 主要企業
12.8.10 市場予測(2025年~2033年
13 日本の3Dプリンティング市場:競合状況
13.1 概要
13.2 市場構造
13.3 市場における各社のポジショニング
13.4 主な成功戦略
13.5 競合ダッシュボード
13.6 企業評価クアドラント
14 主要企業のプロフィール
14.1 企業A
14.1.1 事業概要
14.1.2 提供サービス
14.1.3 事業戦略
14.1.4 SWOT分析
14.1.5 主要ニュースおよびイベント
14.2 企業B
14.2.1 事業概要
14.2.2 提供サービス
14.2.3 事業戦略
14.2.4 SWOT分析
14.2.5 主要ニュースとイベント
14.3 企業C
14.3.1 事業概要
14.3.2 提供サービス
14.3.3 事業戦略
14.3.4 SWOT分析
14.3.5 主要ニュースとイベント
14.4 企業D
14.4.1 事業概要
14.4.2 提供サービス
14.4.3 事業戦略
14.4.4 SWOT分析
14.4.5 主要ニュースとイベント
14.5 企業E
14.5.1 事業概要
14.5.2 提供サービス
14.5.3 事業戦略
14.5.4 SWOT分析
14.5.5 主要ニュースとイベント
これは見本目次であるため、社名は記載されていません。最終報告書には完全なリストが記載されます。
15 日本の3D印刷市場 – 業界分析
15.1 推進要因、阻害要因、および機会
15.1.1 概要
15.1.2 推進要因
15.1.3 阻害要因
15.1.4 機会
15.2 ポーターのファイブフォース分析
15.2.1 概要
15.2.2 買い手の交渉力
15.2.3 売り手の交渉力
15.2.4 競争の度合い
15.2.5 新規参入の脅威
15.2.6 代替品の脅威
15.3 バリューチェーン分析
16 付録
❖本調査レポートの見積依頼/サンプル/購入/質問フォーム❖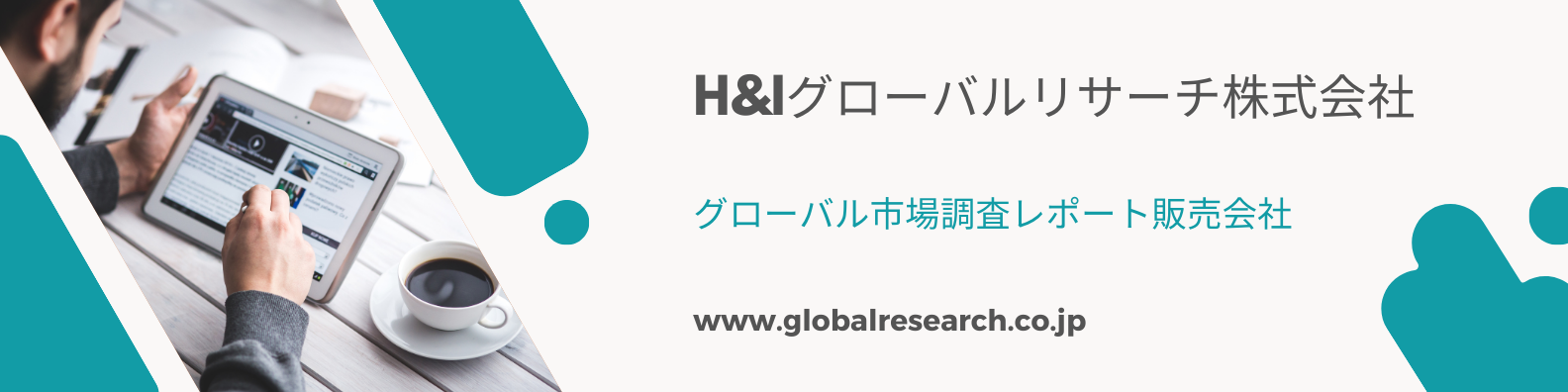